Industrial mixers for Powder Coating & Bonding Premixes
Powder coating
Bonding
Metal bonding
Powder coating
Pigment powder
Effect coatings
Effect pigments
Aluminum pigments
Glimmer
For an optimal color output of pigments. Clean tool changes and highest mixing quality.
What would you like to mix?
In 2 minutes to your mixer.
Stationary mixers and container mixers. Mixing powder coatings perfectly.
Optimum mixing technology is very important in the production of powder and effect coatings. This is because, in addition to the wide range of products and applications, precision and cleanliness in processing are particularly important here.
MIXACO has the optimum mixers and tools as well as extensive expertise in the efficient and careful mixing of pigment powders and powder coatings.
Our specialists are very experienced in the powder coating industry. They know the requirements when dealing with individual pigment formulations and specific formulations.
From this, they work with our customers to develop targeted solutions for the industrial production of high-quality powder coatings. Once MIXACO’s machines are set up for the formulation, production can run perfectly and smoothly over the long term.
All important parameters are already taken into account in extensive test runs. The mixing process focuses on dispersion in order to achieve the best possible color application of the pigments.
This makes it possible to use cost-intensive pigments economically. At the same time, the processing quality can be improved in many areas. For example, effect pigments require very gentle handling due to their filigree design.
The pigments are carefully bonded to the powder coating particles using MIXACO mixers.
Experience the advantages of our industrial mixers for the production of powder coatings:
Advantages
- Mixer with double jacket for cooling
- Mixing container without dead spaces
- Shorter mixing times than with standard mixing systems on the market
- Homogenizing dry & moist formulations to the highest quality
- Realize several process steps in one mixer: mixing, moistening, coating
- High throughputs, fast emptying and rapid formulation switching
- Batch tracing possible
- Very high residual emptying rate
- Variable fill level
- The batch sizes of our container mixers for bonding processes and powder coatings are scalable from 75 to > 2,000 litres and grow with your production capacities
- Intensive and excellent homogenization of the mixing material
- The mixing quality is ensured even with difficult components – for finished products in consistent quality
- Thanks to extremely gentle mixing – without heating where necessary – even the most sensitive paint particles can be homogenized
- Minimal cleaning effort for rapid formulation switching: mixing elements and mixing tools are easily accessible and removable
- Low idle times due to fast and easy cleaning
- Solid and low-maintenance machine technology “Made in Germany” guarantees high availability of the production system
- Specially coated mixing tools for a long service life
- MIXACO mixers are available in various ATEX designs
- Low energy consumption thanks to innovative designs and tools
- Optimal application solutions due to customized tests and mixing processes
- Simple & safe operation of industrial mixers thanks to innovative machine concept
- Special mixer designs with special materials
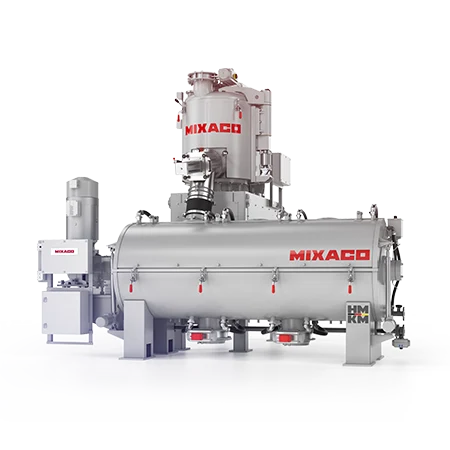
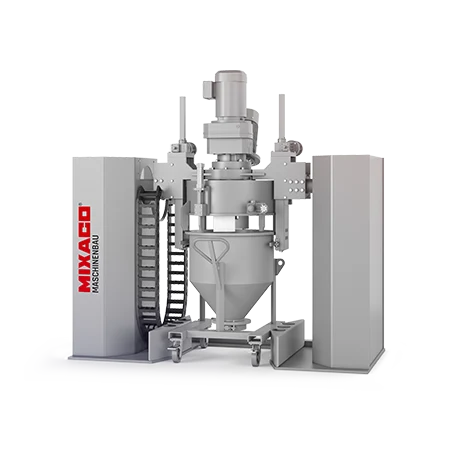
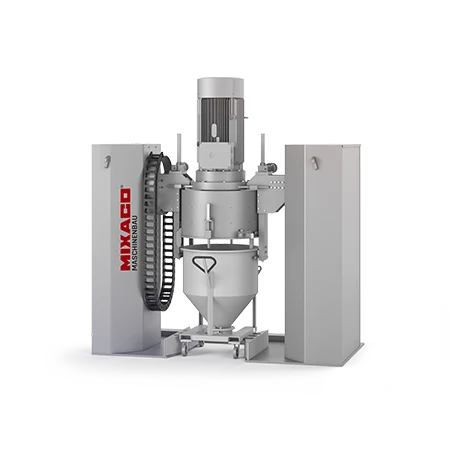
From bonding to effect coatings. We mix all Powder coating premixes and bonded powder coatings.
We supply mixing systems for the development and production of powder coatings in numerous dimensions and batch sizes.
As a leading manufacturer in this market, MIXACO offers maximum efficiency, the highest mixing quality, optimum machine availability and unique know-how for the individual requirements of the powder coating industry.
Coatings can be produced from metal powder for a range of metallic finishes – from silver to gold and with all degrees of gloss and profile. With the addition of metal powders and specialty pigments suitable for thermoplastic polymers.
- Powder coatings
- Bonding
- Metal pigments
- Powder coating
- Effect coatings
- Aluminum pigments
- Glimmer / Mica
- and many more
Procedures and functions. Mixers for the high requirements in the production of various powder coatings.
Applications in the powder coatings industry such as effect coatings, metallic and bonded powder coatings or glimmer constantly require new considerations in terms of raw materials, procedures and work processes.
Our specialists’ decades of experience in the production of powder coatings are also particularly impressive. Where clean tool changes, fast container exchange and the highest mixing quality come together, MIXACO proves its true greatness time and time again.
Our solutions simplify and optimize production in the long term by taking a holistic view of the work processes involved in mixing. Even in small batches, mixing processes can be accelerated and batches of different sizes can be produced more flexibly.
MIXACO has thorough expertise in mixing pigment powders and powder coatings. We are familiar with all methods for all common products and processes in the powder coatings industry. And if you are still looking for a solution for your latest idea, we can step in to help with development right away.
For the production of powder coatings, the extruders must be loaded with premixed material. To do this, all raw materials that are to be loaded into the downstream (injection) machines must first be completely combined into a homogeneous mass.
MIXACO industrial mixers always provide the best alternative to traditional high-speed mixers when production conditions demand a high degree of versatility and many different products are to be mixed with one and the same mixer.
Thanks to the special design, in which the container mixer is divided into two separate units (mixing head + transportable container), the cleaning time between the individual batches and thus the danger of contamination when changing from one production type to the next can be reduced to a minimum.
Mixing, storage and transport are optimized as they are carried out directly in the same containers. These can be easily inserted into a dosing system with both a weigher and a dosing device for emptying into an extruder.
Our container mixers are also ideal for mixing with metallic pigments (metal mixture) after production, guaranteeing the distribution of pigments in a safe, controlled and nitrogen-inert environment.
Additional functions. Mix powder coatings and pigment powders individually.
Our mixers are perfectly adapted to the production of your pigments and powder coatings via various additional options:
- Dust removal
- Temperature measuring
- Ventilation and loading during the mixing process
- Container tempering (external with double jacket)
- Temperature measurement of the mixing material
- Data recording and analysis
- Compatibility with existing systems
- Extended stainless steel design
- Wearing protection for the tools
- Special painting
- Coatings
- AGV (automatic guided vehicle) compatibility (container mixer)
- Container weighing (container mixer)
- ATEX/NEC version
- Remote maintenance
- 360° cloud monitoring (MIXACO Control Center)
Mixer Quotation Configurator: Just 2 minutes to the perfect mixer for your raw materials.
Simply tell us your requirements and we will recommend you the optimum mixer for your raw materials and applications. Use our configurator.
With your details on quantities, mixtures, temperatures, additional functions and other information, we will prepare a customized quotation for you.
Metallic powder coating. Bonding in the production of powder coatings.
The production of metallic powder coatings is best achieved by the bonding process, which is relatively safe and, if carried out correctly, leaves no free metal particles in the powder.
The bonding process can be described as the complete adhesion of metal pigments to the thermosetting base. Problems in connection with separation and agglomeration disappear with the simultaneous possibility of recycling the powders as with normal powder coatings without metal pigments.
The metallic effect is constant even with large product batches and surfaces. The risk of adding pigments, especially those made of aluminium, is resolved by creating a safe basis for the process (inerting with nitrogen) and using the best equipment approved for use in explosive ATEX environments.
The bonding procedure can be divided into different sections:
This is achieved simply by applying heat and softening the powder coating and then mixing the metal pigments until all the particles literally “stick” to the surface of the powder particles.
Turbo mixers are most commonly used to achieve this effect: This involves loading the powder coating and metal pigments into the high-speed turbo mixer (which is usually jacketed to allow some control of the process temperature) and then mixing at high speed for a few minutes.
The mixing energy leads to an increase in the temperature of the powder until the softening temperature (TG: 40 to 60 °C) is reached, which allows the metal pigments to adhere to the surface of the powder. After reaching the end point of the mixing process, the mixture is quickly drained into a cooling device to prevent premature hardening/solidification.
The hot mixture must be cooled down as quickly as possible (25 °C). This is done using a separate low-intensity cooler with a water-cooled jacket, which is sufficient to reduce the temperature of the mixture.
In most cases, the amount of material that is subjected to the bonding process corresponds to a small part of a larger batch, and therefore the cooler can also cool up to 3 batches from the bonding system at the same time.
As the powder coating is exposed to heat during the bonding process and can therefore form lumps, these may need to be removed from the end product. A mesh sieve with 130 -150 microns is usually sufficient for this.
The final requirements for an optimal bonded powder coating are: optimal powder recycling during the application process thanks to the strong bond between the metallic pigments and the bonded powder base; no separation of the powder coating during application by spraying; even application of the metallic effect on the workpiece.
You can find more information at https://de.wikipedia.org/wiki/Powder_coating
Premixing raw materials https://www.interpon.com/us/article/manufacture-powder-coating
All raw materials used in powder coatings are in a solid state when mixed. The polymer and the other ingredients (such as pigments, fillers, crosslinkers, etc.) are precisely weighed and poured into a mixing vessel. The substances are then mixed to produce a homogeneous substance.
This premix is then fed into the extruder, whose cylinder is kept at a precisely defined temperature. The cylinder temperature is set so that the polymer just about liquefies.
If the temperature is too high, this leads to low melt viscosity with low shearing force and poor pigment distribution, meaning that the coating would not have the desired performance properties.
The feed rate at the hopper and the speed of the extruder screw are now set so that the screw is always well filled. By carefully adjusting these three parameters, high shearing forces are maintained so that thorough mixing takes place in the extruder.
The molten extrudate is passed between cooling rollers and emerges as a thin sheet about one millimeter thick before being broken into pieces about 10 to 20 mm in size. https://www.neuman-esser.de/en/company/media/dosing-and-dispersing/
In powder coating preparation, additives such as aluminum oxide (AI2O3) or silicon dioxide (SiO2, silica), i.e. silica, are used to improve the flowability of the solid particles.
The cost of additives in powder coating production can be reduced by improving the dispersion of the additive in the powder coating. This reduces the amount of additives required while maintaining the desired flowability.
Additives in powder coatings include leveling agents, matting agents, structural additives, flowability agents and waxes that influence the surface. Most powder coating additives are combined with the premix and incorporated into the formulation during extrusion.
However, additives that influence the flowability, such as aluminum oxide and silica, are only mixed with the powder coating after extrusion. These post-blend additives are added either before, during or after grinding [1].
Flowability is particularly important for the application of the powder coating. The additives, mainly aluminum oxide and silica, facilitate the transport of the powder coating and prevent surface defects and spitting during the application of the powder coating. Aluminum oxide also improves storage stability, prevents powder coatings from absorbing moisture and improves the edge coating of the substrates. In addition, aluminum oxide increases the electrostatic positive chargeability of tribo powders [2].
As a rule, approx. 20 t to 50 t of additives are required per 10,000 t of powder coating. The aim is to reduce the amount of aluminum oxide or silica added to the powder coating during production.
The quality of the powder coating is also to be improved. White spots on the paint surface caused by agglomeration in the powder coating should be reduced or avoided.
Service & Support for our industrial mixers. You can rely on us and our experienced technicians.
More than mixers. Holistic customer care for over 55 years.
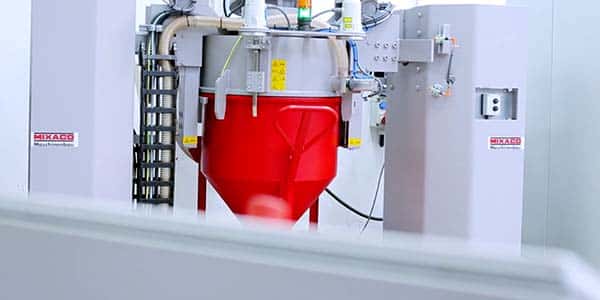
Test mixer free of charge and without obligation
Test our mixers in our test center – with your own raw materials, of course.
Learn More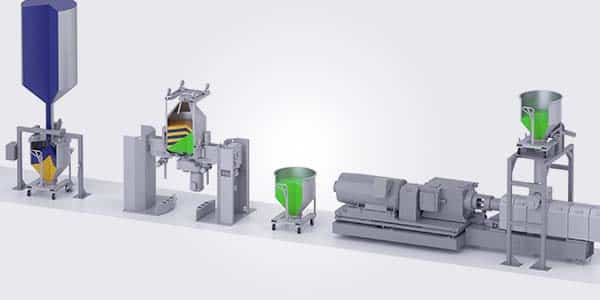
Mix & Process Consulting
Have your mixing process checked by our mixing professionals – free of charge & no obligation.
Learn More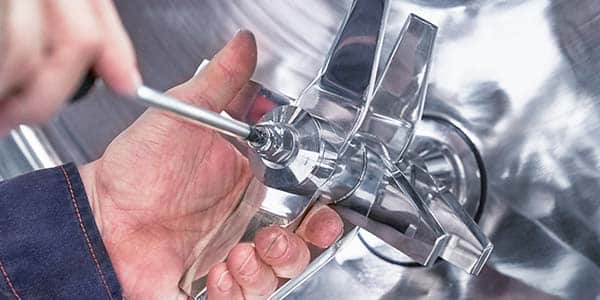
The MIXACO Technical Center
In our test centers we can optimize all parameters for your compound.
Learn More