MIXACO Double Cone Mixer
The MIXACO tumbler mixer. Faster mixing due to interchangeable containers.
Benefits at a glance. Gentle and cost-efficient homogenization.
The easy handling and the good accessibility of all machine components for cleaning make the tumbler mixer DCM an economical solution for simple mixing tasks.
- MIXACO containers with mobile pallet available on site can be used if necessary
- Gentle homogenization of the product
- No active mixing tools, thus minimal energy input
- Mix up to 2,000 liters per batch
- Painted steel or stainless steel version
- Free-standing double cone mixer
- Various safety enclosures such as safety grids, safety doors or light barriers
- Containers can be used for downstream processes – no decanting necessary
- Higher availability of the mixer due to cleaning of the mixing container outside the mixer
Functionality. The new Double Cone Tumbler Mixer.
The double cone mixer consists of two mobile mixing vessels of equal size and the tumbling mixer. For the mixing process, an empty mixing container is moved by the operator to the tumbling mixer.
The container, which is loose on the driving pallet, is lifted to the mixing head by the pneumatic lift and securely locked there.
After swiveling the rotatable mixing head by 180°, the second mobile mixing container with the material to be mixed is lifted and locked to the mixing head in the same way.
The moving pallet remains in the mixer. By means of the PLC control, the mixing process is now started program-controlled by the operator.
After starting, both mixing vessels rotate 360° at adjustable speed around the swivel axis of the mixing head.
Due to fixed mixing segments in the mixing head, the material is optimally distributed and deflected during the tumbling motion. After the preset mixing time has elapsed, the mixing process is stopped.
After unlocking, the lower container with the mixed material can be lowered onto the driving pallet and removed from the mixer by the operator. The mixed material can be emptied via the outlet at the lower end of the mixing container.
The loose container on the mobile pallet is lifted to the mixing head by the pneumatic lift and securely locked there. After swiveling the rotatable mixing head by 180°, the second mobile mixing container with the material to be mixed is lifted to the mixing head and locked in the same way.
After starting, both mixing vessels rotate 360° at adjustable speed around the swivel axis of the mixing head.
In the cleaning position, no container is coupled to the mixing head ring. This can then be easily cleaned by the operator.
Here you can see the double cone mixer in profile view with two coupled mixing containers.
What would you like to mix?
In 2 minutes to your mixer.
Control. Safe, efficient and economical.
The control of the double cone mixer is based on a Siemens S7 PLC and meets today’s requirements for safety, efficiency and economy. The development and programming of the control system from a single source ensures optimum integration of the mixer components. Alternatively, it is also possible to use Allen-Bradley components (incl. Panelview operating unit).
The control can also be designed according to UL / NEMA. In addition, the control can be equipped with an interface for data exchange to a higher-level control.
Siemens TP700
Up to 99 mixing programs, each with ten working steps, can be created in tabular form via the TP700 touch control panel. Data acquisition and storage of the measured values takes place.
Allen Bradley
Control to UL / NEMA standards with an Allen Bradley PLC and Panelview control panel is also possible.
Details. Sophisticated technology.
The double cone mixer can process batch sizes from 2,000 liters. The production capacity can thus be up to over 6,000 liters per hour. The diameter of the mixing drum is 0.3 – 3.6 m, depending on the size.
Due to the fixed mixing segment, the material is optimally deflected and swirled during tumbling. An even distribution of the materials involved in the mixing process is thus ensured.
The rotary union ensures safe transport of the operating media (including compressed air) to the rotating mixing head.
The moving pallet, which has proven itself in practice, ensures safe transport of the container from the charging station to the DCM double cone mixer or to the discharging device. At the same time, the moving pallet is used to pick up and transport the container after mixing.
The lifting cylinder enables the container to be lifted with pinpoint accuracy from the moving pallet to the mixing head and back again to the moving pallet.
The remote maintenance module allows fast and secure access to the control system of the mixing plants via a VPN tunnel to enable fast diagnosis and repair by our service department in the event of a malfunction. Service calls on site can be avoided in this way.
Mixing Methods. Maximum Functionality.
Our double cone mixer offers best mixing quality for many products and applications. This innovative tumbler mixer delivers optimum mixing results, e.g. for PVC, powder coating, masterbatches and many more.
Applicable as:
- Granulate mixer
- Powder mixer
- Tumbling mixer
- Cone mixer
- Batch mixer
The double cone mixer as a container mixer.
The MIXACO double cone mixer is a very flexible cone mixer that can process up to 2,000 liters per batch in the double mixing vessels.
Additional features. From ATEX to remote maintenance.
MIXACO conical mixers are available in various shapes and sizes and are suitable for countless mixing techniques and processing methods. Cone mixers without base plate and guide fork are possible – for simplified handling and improved hygiene.
Via various options, our conical mixers are perfectly adapted to the processing of your raw materials:
- Dust removal with replaceable filter bags
- Temperature measurement
- Integrated weighing
- Ventilation and feeding during the mixing process
- Dosing / spraying / injection of liquids and gases during the mixing process
- Mixing head cooling
- Sampling
- ATEX versions
- Double jacket design for temperature control of the mixing material
- Data recording and evaluation
- Hygienic design
- Cleaning wet or dry
- Cone mixer design according to GMP, WIP, CIP
- Cooling, heating, drying
- Water-cooled motors and tools
- Individual mixing tool geometries
- Wear-resistant designs against abrasion, corrosion and adhesion
- Dust-resistant machine components
- Individual sealing variants
- Remote maintenance
- 360° cloud monitoring (MIXACO Control Center)
Double Cone Mixer sizes. We gladly advise you.
Sizes | Usable Volume liter | Batchsize kg | Mixing Time min/Batch |
---|---|---|---|
DCM 450 | 450 | 225 | 3-6 |
DCM 600 | 600 | 300 | 3-6 |
DCM 800 | 800 | 400 | 3-6 |
DCM 1000 | 1000 | 500 | 3-6 |
DCM 1300 | 1300 | 650 | 3-6 |
DCM 2000 | 2000 | 1000 | 3-6 |
Parameter
Bulk Density: 0.5 kg/l
Filling Level: max. 50%
Charging: manually
Please contact us for other sizes.
As the inventor of the container mixer, we at MIXACO are committed to innovation in industrial mixing technology.
Container Mixer Accessories. For efficient Workflows.
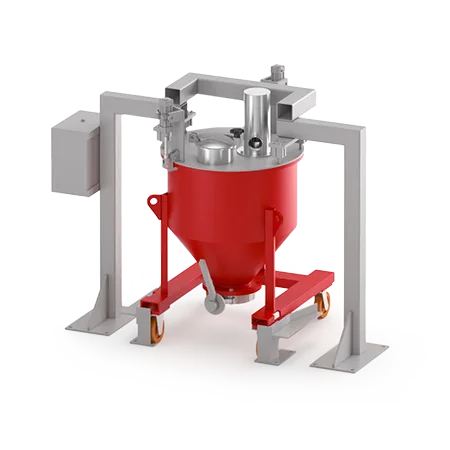

Discharge Stations
Dust-free discharge of the mixed material into downstream further processing steps.
Learn More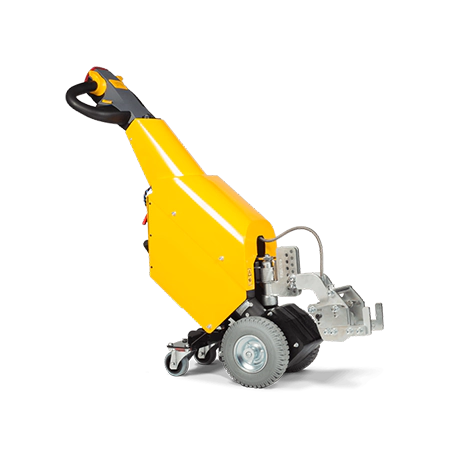
Service & support for our mixers. You can rely on our experienced technicians.
Get quote for the perfect mixer in 2 minutes.
More than mixers. Holistic customer care for over 55 years.
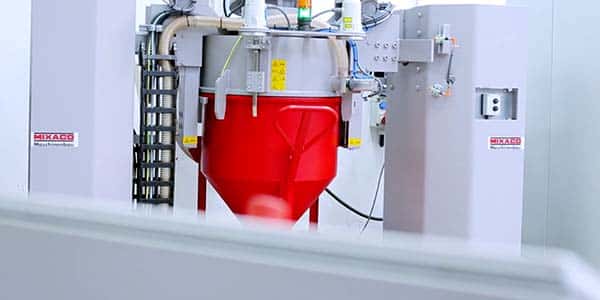
Test mixer free of charge and without obligation
Test our mixers in our test center – with your own raw materials, of course.
Learn More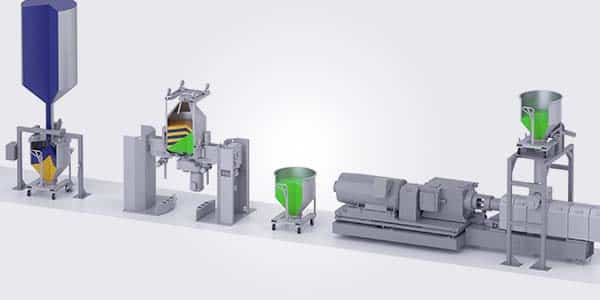
Mix & Process Consulting
Have your mixing process checked by our mixing professionals – free of charge & no obligation.
Learn More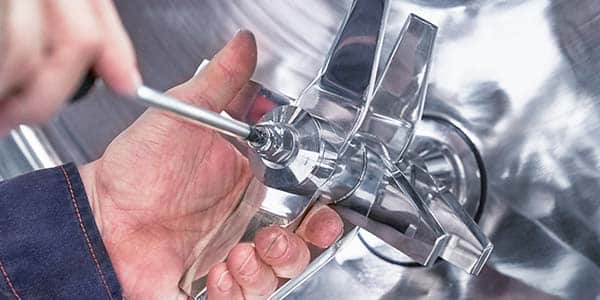
The MIXACO Technical Center
In our test centers we can optimize all parameters for your compound.
Learn More